As dental technicians, the precision and quality of our work are paramount. From a single crown to a complex RPD framework, the success of a metal prosthetic often hinges on the critical step of casting. Choosing the right casting machine for your lab isn’t just about buying equipment; it’s an investment in quality, efficiency, and ultimately, patient satisfaction. But with different technologies available – traditional manual methods, air-cooled induction, and water-cooled induction – how do you decide which is best suited for your lab’s specific needs?
This guide will walk you through the options, comparing their strengths and weaknesses, to help you make an informed decision.
Why Your Casting Machine Choice Matters
The casting machine directly impacts several key areas of your lab’s operation:
- Restoration Quality: Influences casting density, porosity, surface texture, marginal fit, and alloy integrity (e.g., preventing oxidation).
- Efficiency & Workflow: Affects heating time, cooling time, potential for continuous operation, and ease of use.
- Material Versatility: Determines the range of alloys you can reliably cast (base metals, noble, high-noble, titanium alloys).
- Consistency & Remake Rate: Impacts the predictability of results, directly affecting profitability.
- Safety & Lab Environment: Relates to operational hazards, noise levels, and heat emission.
- Cost: Includes initial investment, running costs (energy, consumables, maintenance), and potential lifespan.
The Contenders: An Overview
Let’s break down the three main types of casting equipment found in dental labs:
- Manual Casting (e.g., Torch + Centrifugal/Vacuum): The traditional method. Metal is typically melted using a gas-oxygen torch (like acetylene or propane) and then cast into the investment mold using a spring-wound or electric centrifugal machine, or sometimes vacuum pressure.
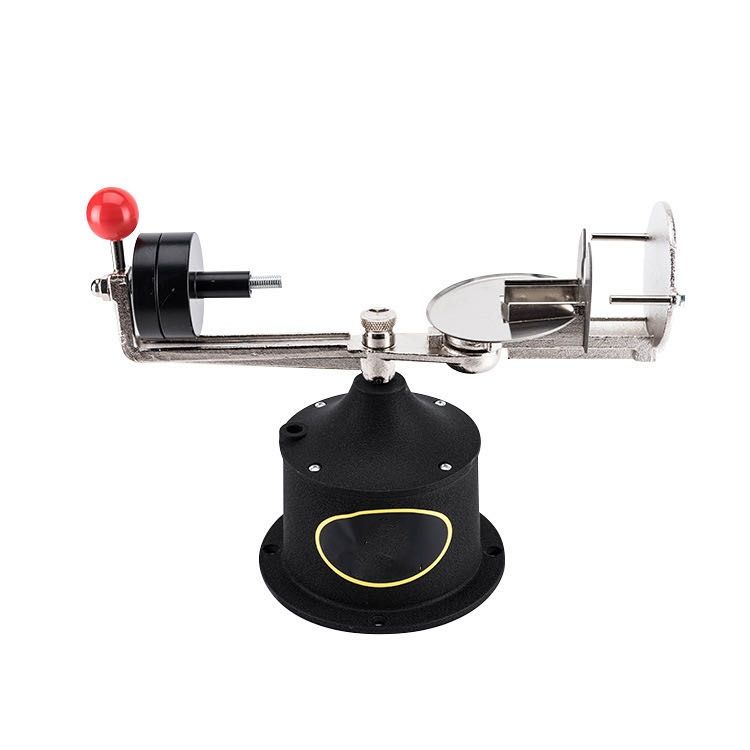
manual handpiece operation the casting procedure
- Air-Coled Electric Induction Casting: Uses electromagnetic induction to heat the metal alloy within a crucible. The heat generated in the machine’s components (especially the induction coil and electronics) is dissipated using fans blowing air over heat sinks. Often integrates centrifugal or vacuum casting.
- Water-Cooled Electric Induction Casting: Also uses electromagnetic induction for heating. However, it employs a liquid cooling system (usually distilled water or a coolant mixture) circulated by a pump through internal channels and an external radiator (or connected to a central chilling system) to remove heat much more efficiently. Typically integrates centrifugal or vacuum casting.
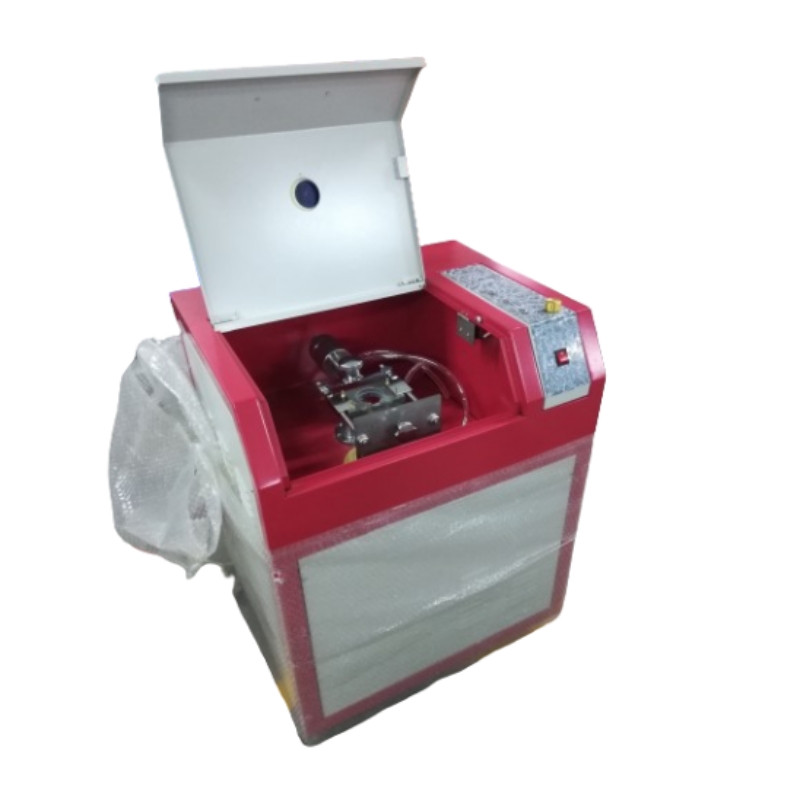
recycable water-cooling builded in the induction casting equipment
The following video shows the technician open the side door, and connect the inlet and outlet water pipe, which will be powered by the build in water pump for recycable cooling the casting accessories during the induction and casting procedure.
Deep Dive Comparison: Manual vs. Air-Cooled vs. Water-Cooled Induction
Feature | Manual (Torch + Centrifugal/Vacuum) | Air-Cooled Induction | Water-Cooled Induction |
---|---|---|---|
Heating Method | Open Flame (Gas/Oxygen) | Electromagnetic Induction | Electromagnetic Induction |
Temperature Control | Highly Skill-Dependent; Visual Estimation | Good; Electronic Control, Relatively Precise | Excellent; Electronic Control, Very Precise & Stable |
Heating Speed | Slowest | Fast | Fast (Potentially Fastest/Highest Power) |
Atmosphere Control | Difficult; Risk of Oxidation/Gas Pickup | Good (Crucible helps); Vacuum options improve further | Excellent (Crucible + Vacuum/Argon options readily available) |
Casting Quality | Variable; Skill-Dependent; Higher Porosity/Oxide Risk | Good to Excellent; Consistent; Lower Porosity Risk | Excellent; Highly Consistent; Minimal Porosity/Oxides |
Consistency | Low to Medium | High | Very High |
Cooling System | N/A (for heat source) | Air (Fans + Heat Sinks) | Liquid (Water/Coolant + Pump + Radiator) |
Duty Cycle/Perf. | Limited by Operator & Centrifuge Reset | Good; May need cooldown in heavy use/hot climates | Excellent; Supports Continuous Use & High Power Output |
Ease of Use | Difficult; Requires Significant Skill & Experience | Medium; Requires Training but Process is Automated | Medium; Similar to Air-Cooled + Coolant System Management |
Skill Required | Very High | Medium | Medium |
Safety | Lower (Open Flame, Hot Parts, Manual Handling) | Medium (Electrical, Hot Parts, Shielded Process) | Medium to High (Shielded Process, Coolant Handling) |
Material Versatility | Wide Range (with skill); Difficult for Reactive Metals | Wide Range; Good for Base & Noble Metals | Widest Range; Ideal for High-Fusing Alloys & Titanium |
Maintenance | Medium (Torch Tips, Gas Lines, Centrifuge Mechanics) | Medium (Fan Cleaning, General Electrics) | Medium to High (Coolant Check/Change, Pump, Radiator, Lines) |
Initial Cost | Lowest | Medium | Highest |
Running Cost | Medium (Gas Consumables) | Medium (Electricity) | Medium to High (Electricity, Coolant Maintenance) |
Noise Level | High (Torch Roar, Centrifuge) | Medium to High (Fans) | Medium (Pump Noise, Quieter than heavy fans usually) |
Heat Emission | High (Open Flame) | Medium (Heat Sink Radiation) | Lower (Most heat removed via coolant) |
Export to Sheets
Making Your Choice: A Practical Guide
There’s no single “best” machine – the right choice depends entirely on your lab’s specific situation. Ask yourself these questions:
- What’s your budget?
- Tight Budget/Low Volume: Manual might seem appealing initially, but factor in skill requirements and potential remake costs. Air-cooled induction is often a good middle ground.
- Investment Focused: Water-cooled offers top performance and longevity, justifying a higher upfront cost for busy labs demanding quality.
- What’s your workload?
- Low Volume/Occasional Casting: Manual or Air-cooled might suffice.
- Medium to High Volume/Frequent Casting: Induction is far more efficient. Water-cooled handles continuous work better than air-cooled, preventing bottlenecks.
- What alloys do you cast most often?
- Mainly Base Metals (CoCr, NiCr), Noble Alloys: Air-cooled induction usually handles these well.
- High-Fusing Alloys, Titanium, Demanding Noble Alloys: Water-cooled induction offers the stable high temperatures and controlled atmosphere often required. Manual methods are generally unsuitable for titanium due to contamination risk.
- How critical are consistency and minimizing porosity?
- Utmost Importance (e.g., Complex Implant Bars, Precision Fits): Induction casting (especially water-cooled with vacuum/argon) provides the most control and best results.
- Standard Requirements: Air-cooled induction offers a significant improvement over manual methods.
- What is the skill level of your technicians?
- Highly Experienced Technician Available for Casting: Manual can work, but still has limitations.
- Variable Skill Levels/Training New Staff: Induction machines are much easier to learn and use consistently, reducing reliance on individual “golden hands.”
- What are your lab’s space and utility constraints?
- Limited Space/No Easy Water Access: Air-cooled might be more practical (though some water-cooled units have self-contained reservoirs).
- Adequate Space & Utilities: Water-cooled is feasible. Consider power requirements for all induction units. Manual requires proper ventilation and gas storage/handling.
Conclusion: Matching Technology to Your Needs
Choosing a casting machine is a strategic decision.
- Manual casting remains an option for labs with very low budgets and highly skilled technicians who understand its limitations, but it struggles with consistency, efficiency, and modern alloy demands.
- Air-cooled induction casting represents a significant leap forward, offering speed, control, and consistency at a moderate price point. It’s a versatile workhorse for many labs handling common alloys.
- Water-cooled induction casting is the premium choice for labs prioritizing maximum performance, the ability to handle any alloy reliably, high throughput, and long-term durability, especially under demanding conditions. The superior cooling ensures stable operation and protects the investment.
Evaluate your lab’s current and future needs carefully. Consider the types of restorations you produce, the volume of work, the materials you use, and your budget. While the initial cost is a factor, also weigh the long-term benefits of efficiency, reduced remakes, and enhanced quality that a modern induction casting machine, particularly a water-cooled model for demanding applications, can bring to your workflow.
Investing wisely in your casting technology is investing in the foundation of countless successful restorations. Choose the powerhouse that best fits your lab’s unique requirements.
Reference: the advaced induction dental casting machine, designed with build in water pump for recycing the cooling effect on the casting container. Product url: https://www.dentallabshop.com/product/dental-alloy-precision-casting-machine/